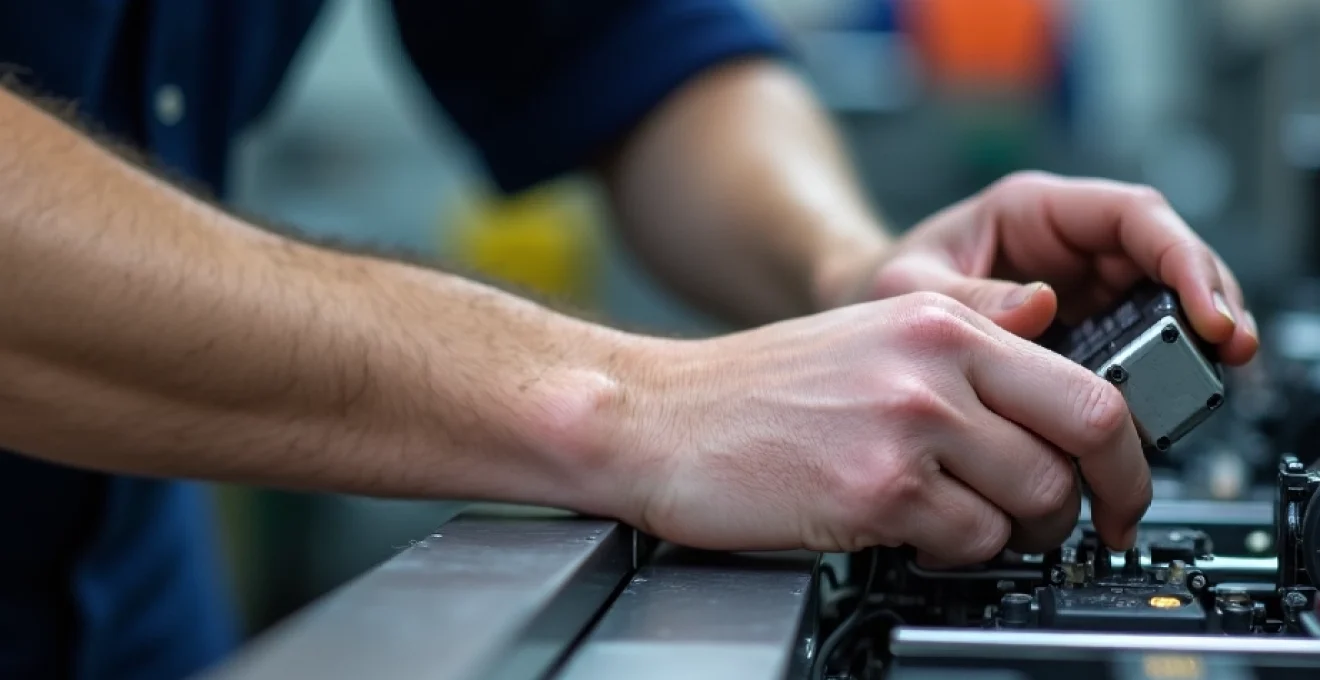
La manutenzione preventiva rappresenta un approccio proattivo alla gestione delle attrezzature e degli impianti industriali. Questa strategia mira a prevenire guasti e malfunzionamenti prima che si verifichino, garantendo così una maggiore affidabilità operativa e una riduzione dei costi a lungo termine. A differenza della manutenzione reattiva, che interviene solo dopo un guasto, la manutenzione preventiva si basa su interventi pianificati e regolari per mantenere le apparecchiature in condizioni ottimali.
L'importanza di questa pratica non può essere sottovalutata nel contesto industriale moderno, dove l'efficienza operativa e la minimizzazione dei tempi di inattività sono cruciali per la competitività aziendale. Implementando un programma di manutenzione preventiva efficace, le organizzazioni possono non solo prolungare la vita utile dei loro asset, ma anche migliorare la sicurezza sul lavoro, ottimizzare le prestazioni delle macchine e ridurre significativamente i costi operativi.
Tecniche di manutenzione preventiva per aumentare l'efficienza operativa
Per massimizzare l'efficacia della manutenzione preventiva, è essenziale adottare un approccio multifaceted che includa diverse tecniche complementari. Queste strategie lavorano in sinergia per creare un sistema di manutenzione robusto e proattivo, capace di anticipare e prevenire problemi prima che si trasformino in guasti costosi.
Ispezioni periodiche per identificare potenziali problemi
Le ispezioni periodiche costituiscono il fondamento di qualsiasi programma di manutenzione preventiva efficace. Queste verifiche regolari permettono di identificare segni precoci di usura, danni o malfunzionamenti prima che si trasformino in problemi più gravi. Durante queste ispezioni, i tecnici specializzati esaminano attentamente ogni componente critico, cercando anomalie come:
- Segni di corrosione o deterioramento
- Parti allentate o disallineate
- Rumori o vibrazioni insoliti
- Perdite di fluidi o gas
- Anomalie nelle temperature operative
L'implementazione di un sistema di ispezioni regolari non solo aiuta a prevenire guasti improvvisi, ma fornisce anche dati preziosi sullo stato generale delle attrezzature nel tempo. Questi dati possono essere utilizzati per affinare ulteriormente il programma di manutenzione e prendere decisioni informate su quando sostituire o aggiornare i componenti.
Lubrificazione regolare dei componenti meccanici critici
La lubrificazione adeguata è fondamentale per il corretto funzionamento e la longevità di molti componenti meccanici. Una lubrificazione insufficiente può portare a un aumento dell'attrito, surriscaldamento e usura accelerata, mentre una lubrificazione eccessiva può causare accumuli di sporcizia e problemi di tenuta. È quindi cruciale stabilire un programma di lubrificazione ottimizzato per ciascun componente.
Un programma di lubrificazione efficace dovrebbe includere:
- Selezione del lubrificante appropriato per ogni applicazione
- Determinazione degli intervalli di lubrificazione ottimali
- Formazione del personale sulle tecniche di lubrificazione corrette
- Monitoraggio del consumo di lubrificante per identificare anomalie
- Utilizzo di tecnologie avanzate come la lubrificazione automatizzata quando appropriato
Implementando queste pratiche, è possibile ridurre significativamente l'usura dei componenti, migliorare l'efficienza energetica e prolungare la vita utile delle attrezzature.
Calibrazione degli strumenti di misurazione essenziali
La precisione degli strumenti di misurazione è cruciale per garantire la qualità del prodotto e l'efficienza dei processi produttivi. La calibrazione regolare di questi strumenti è una componente essenziale della manutenzione preventiva, assicurando che le letture siano accurate e affidabili nel tempo.
Un programma di calibrazione efficace dovrebbe:
- Identificare tutti gli strumenti di misurazione critici
- Stabilire intervalli di calibrazione basati sulle specifiche del produttore e l'uso effettivo
- Documentare tutte le procedure di calibrazione e i risultati
- Formare il personale sulle corrette procedure di calibrazione
- Implementare un sistema di tracciabilità per gestire le scadenze di calibrazione
La calibrazione regolare non solo migliora la precisione delle misurazioni, ma può anche aiutare a identificare precocemente problemi con le attrezzature, contribuendo così all'efficacia complessiva del programma di manutenzione preventiva.
Vantaggi economici di una strategia di manutenzione proattiva
L'adozione di una strategia di manutenzione proattiva, basata sulla prevenzione piuttosto che sulla reazione ai guasti, può portare a significativi vantaggi economici per le organizzazioni. Questi benefici si manifestano non solo in termini di riduzione dei costi diretti di manutenzione, ma anche attraverso un miglioramento complessivo dell'efficienza operativa e della produttività.
Riduzione dei costi associati ai fermi macchina
I fermi macchina non pianificati rappresentano uno dei costi più significativi per le aziende manifatturiere. Questi eventi non solo interrompono la produzione, ma possono anche portare a danni alle attrezzature, sprechi di materiali e ritardi nelle consegne ai clienti. La manutenzione preventiva mira a ridurre drasticamente l'incidenza di questi costosi fermi macchina.
Un'analisi condotta su diverse industrie ha mostrato che l'implementazione di un programma di manutenzione preventiva efficace può ridurre i tempi di fermo non pianificati fino al 45%. Questo si traduce in un aumento significativo della produttività e in una riduzione dei costi operativi. Inoltre, la capacità di pianificare gli interventi di manutenzione permette di ottimizzare l'allocazione delle risorse e minimizzare l'impatto sulla produzione.
La manutenzione preventiva non è un costo, ma un investimento che si ripaga rapidamente attraverso una maggiore affidabilità e produttività degli impianti.
Prolungamento della vita utile delle attrezzature
Una delle conseguenze più dirette della manutenzione preventiva è l'estensione della vita utile delle attrezzature. Intervenendo regolarmente per mantenere le macchine in condizioni ottimali, si previene l'usura accelerata e si riduce il rischio di guasti catastrofici che potrebbero richiedere la sostituzione completa dell'apparecchiatura.
Studi hanno dimostrato che un programma di manutenzione preventiva ben implementato può aumentare la vita utile delle attrezzature del 20-40%. Questo si traduce in un ritorno sull'investimento significativo, considerando il costo elevato di molte apparecchiature industriali. Inoltre, la sostituzione meno frequente delle attrezzature contribuisce a ridurre i costi di capitale a lungo termine e migliora la sostenibilità ambientale dell'azienda.
Ottimizzazione dell'utilizzo delle risorse di manutenzione
Un approccio preventivo alla manutenzione permette una migliore pianificazione e allocazione delle risorse. Invece di reagire costantemente alle emergenze, il personale di manutenzione può lavorare in modo più efficiente, seguendo un programma strutturato di interventi. Questo non solo migliora la produttività del team di manutenzione, ma riduce anche lo stress e il rischio di errori dovuti alla pressione delle situazioni di emergenza.
L'ottimizzazione delle risorse di manutenzione si traduce in:
- Riduzione delle ore di straordinario
- Migliore gestione dell'inventario dei pezzi di ricambio
- Maggiore efficacia degli interventi di manutenzione
- Miglioramento della sicurezza sul lavoro
- Aumento della soddisfazione e della retention del personale tecnico
Implementando un sistema di gestione della manutenzione computerizzato ( CMMS
), le aziende possono ulteriormente ottimizzare la pianificazione e l'esecuzione delle attività di manutenzione, garantendo che le risorse siano utilizzate nel modo più efficiente possibile.
Implementazione di un programma di manutenzione preventiva efficace
L'implementazione di un programma di manutenzione preventiva efficace richiede un approccio sistematico e ben pianificato. Non si tratta semplicemente di eseguire controlli periodici, ma di creare un sistema integrato che coinvolga tutte le parti dell'organizzazione. Un programma ben strutturato può trasformare radicalmente l'efficienza operativa di un'azienda.
Definizione di checklist dettagliate per ogni attrezzatura
Il primo passo verso un programma di manutenzione preventiva efficace è la creazione di checklist dettagliate per ogni tipo di attrezzatura. Queste liste devono essere specifiche e complete, coprendo tutti gli aspetti critici di ciascuna macchina. La creazione di queste checklist richiede una collaborazione stretta tra il personale di manutenzione, gli operatori delle macchine e i produttori delle attrezzature.
Una checklist efficace dovrebbe includere:
- Punti di ispezione visiva
- Parametri operativi da verificare
- Intervalli di lubrificazione e tipo di lubrificante
- Componenti da sostituire periodicamente
- Procedure di test e calibrazione
L'utilizzo di checklist standardizzate non solo assicura che tutte le attività di manutenzione necessarie vengano eseguite, ma facilita anche la formazione del personale e la raccolta di dati coerenti nel tempo.
Formazione del personale sulle procedure di manutenzione
Un programma di manutenzione preventiva è efficace solo quanto le persone che lo implementano. La formazione del personale è quindi un elemento critico per il successo. Questa formazione deve coprire non solo le procedure tecniche specifiche, ma anche l'importanza della manutenzione preventiva e come essa si integra nella strategia complessiva dell'azienda.
Un programma di formazione completo dovrebbe includere:
- Introduzione ai principi della manutenzione preventiva
- Formazione specifica sulle procedure per ogni tipo di attrezzatura
- Tecniche di raccolta e analisi dei dati
- Utilizzo del sistema CMMS
- Sicurezza durante le operazioni di manutenzione
Investire nella formazione continua del personale non solo migliora l'efficacia del programma di manutenzione, ma aumenta anche la motivazione e la soddisfazione dei dipendenti, riducendo il turnover e migliorando la qualità complessiva del lavoro.
Monitoraggio continuo delle prestazioni delle macchine
Il monitoraggio continuo delle prestazioni delle macchine è essenziale per un programma di manutenzione preventiva efficace. Questo monitoraggio può variare da semplici controlli visivi e registrazioni manuali a sistemi sofisticati di monitoraggio in tempo reale basati su sensori e analisi dei dati.
Un sistema di monitoraggio efficace dovrebbe:
- Raccogliere dati su parametri chiave come temperature, vibrazioni, consumi energetici
- Analizzare i trend per identificare deviazioni dalle prestazioni normali
- Generare alert automatici quando vengono rilevate anomalie
- Fornire report dettagliati per supportare il processo decisionale
- Integrare i dati con il sistema CMMS per ottimizzare la pianificazione della manutenzione
L'implementazione di un sistema di monitoraggio avanzato può sembrare costosa inizialmente, ma il ritorno sull'investimento in termini di prevenzione dei guasti e ottimizzazione delle prestazioni è spesso significativo.
Tecnologie innovative per la manutenzione predittiva delle apparecchiature
L'evoluzione tecnologica sta trasformando rapidamente il campo della manutenzione industriale, portando a nuove possibilità nella prevenzione dei guasti e nell'ottimizzazione delle prestazioni delle apparecchiature. La manutenzione predittiva, in particolare, sta emergendo come un approccio altamente efficace, che va oltre la semplice prevenzione per anticipare con precisione quando un componente potrebbe guastarsi.
Le tecnologie chiave che stanno guidando questa rivoluzione includono:
- Sensori IoT (Internet of Things) per il monitoraggio in tempo reale
- Analisi dei big data per identificare pattern e tendenze
- Intelligenza artificiale e machine learning per previsioni accurate
- Realtà aumentata per assistere i tecnici durante gli interventi
- Digital twins per simulare e ottimizzare le prestazioni delle macchine
Queste tecnologie non solo migliorano la precisione e l'efficacia della manutenzione, ma permettono anche di passare da un approccio basato su intervalli fissi a uno basato sulle reali condizioni delle apparecchiature. Ciò si traduce in una riduzione significativa dei costi di manutenzione e in un aumento dell'affidabilità operativa.
L'adozione di tecnologie predittive può ridurre i costi di manutenzione fino al 30% e aumentare la disponibilità delle macchine del 10-20%.
L'implementazione di queste tecnologie richiede un investimento iniziale in hardware, software e formazione, ma il ritorno sull'investimento può essere sostanziale, con molte aziende che riportano un ROI di 3-5 volte l'investimento iniziale nel giro di pochi anni.
Impatto della manutenzione preventiva sulla sicurezza dei lavoratori
Oltre ai vantaggi economici e operativi, la manutenzione preventiva gioca un ruolo cruciale nel migliorare la sicurezza sul lavoro. Attrezzature ben mantenute sono meno propense a guasti improvvisi che potrebbero mettere in pericolo gli operatori. Inoltre, interventi di manutenzione pianificati permettono di eseguire le operazioni in condizioni controllate, riducendo il rischio di incidenti.
I principali benefici in termini di sicurezza includono:
- Riduzione del rischio di incidenti dovuti a malfunzionamenti
- Miglioramento delle condizioni di lavoro attraverso la manutenzione di sistemi di sicurezza
- Diminuzione dello stress degli operatori legato a guasti imprevisti
- Maggiore conformità alle normative sulla sicurezza
- Creazione di una cultura della sicurezza proattiva
Un'analisi condotta su diverse industrie ha mostrato che l'implementazione di un programma di manutenzione preventiva efficace può ridurre gli incidenti sul lavoro fino al 30%. Questo non solo protegge i lavoratori, ma riduce anche i costi associati a infortuni, assenze e potenziali controversie legali.
La sicurezza non è un costo, ma un investimento che si ripaga in termini di produttività, morale dei dipendenti e reputazione aziendale.
Implementare un programma di manutenzione preventiva richiede un impegno significativo in termini di risorse e cambio di mentalità. Tuttavia, i benefici a lungo termine in termini di efficienza operativa, riduzione dei costi e, soprattutto, miglioramento della sicurezza dei lavoratori, rendono questo approccio non solo consigliabile, ma essenziale per qualsiasi azienda che miri all'eccellenza operativa e alla sostenibilità a lungo termine.
La manutenzione preventiva rappresenta un pilastro fondamentale per le moderne strategie di gestione degli asset industriali. Combinando tecniche tradizionali con tecnologie innovative, le aziende possono ottimizzare le prestazioni delle loro attrezzature, ridurre i costi operativi e creare un ambiente di lavoro più sicuro e produttivo. L'investimento in un programma di manutenzione preventiva ben strutturato non è solo una scelta saggia dal punto di vista economico, ma un imperativo strategico per rimanere competitivi nel panorama industriale in rapida evoluzione.