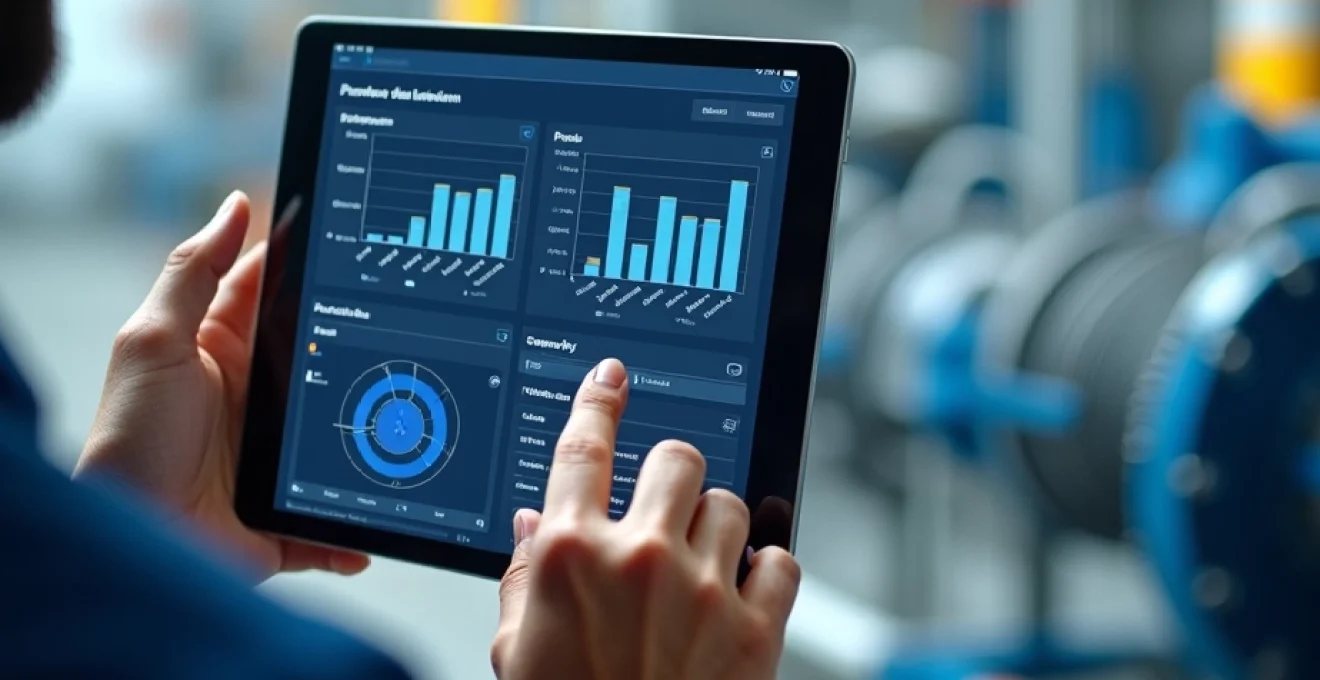
Nel mondo industriale moderno, la manutenzione annuale degli impianti rappresenta un pilastro fondamentale per garantire prestazioni costanti e affidabilità operativa. Con l'evoluzione tecnologica e l'incremento della complessità dei sistemi produttivi, le strategie manutentive hanno subito una profonda trasformazione, passando da approcci reattivi a metodologie proattive e predittive. Questa evoluzione non solo migliora l'efficienza operativa, ma impatta significativamente sulla redditività aziendale e sulla sicurezza degli ambienti di lavoro.
Cicli di manutenzione programmata per impianti industriali
I cicli di manutenzione programmata rappresentano il cuore di una strategia manutentiva efficace per gli impianti industriali. Questi programmi sono progettati per anticipare e prevenire i guasti, riducendo i tempi di fermo macchina non pianificati e ottimizzando le risorse. La pianificazione dei cicli manutentivi si basa su un'attenta analisi dei dati storici, delle raccomandazioni dei produttori e delle specifiche condizioni operative di ciascun impianto.
Un aspetto cruciale nella definizione dei cicli di manutenzione è la categorizzazione degli asset in base alla loro criticità per il processo produttivo. Gli impianti vengono classificati in funzione dell'impatto che un loro eventuale guasto avrebbe sull'intera catena produttiva, permettendo di allocare le risorse manutentive in modo più efficiente. Ad esempio, un componente critico come un compressore principale potrebbe richiedere interventi più frequenti rispetto a un'unità di supporto secondaria.
La frequenza degli interventi manutentivi viene determinata considerando diversi fattori, tra cui:
- L'età e lo stato di usura dell'impianto
- Le condizioni ambientali e operative
- I requisiti normativi e di sicurezza
- L'analisi costi-benefici degli interventi
L'implementazione di cicli di manutenzione programmata richiede un approccio sistematico e una gestione accurata delle attività. L'utilizzo di software CMMS (Computerized Maintenance Management System) è diventato essenziale per orchestrare efficacemente questi processi, consentendo una pianificazione dettagliata, il tracciamento degli interventi e l'analisi delle performance manutentive.
Diagnostica predittiva e analisi dei dati per ottimizzare gli interventi
La diagnostica predittiva rappresenta un salto qualitativo nella gestione della manutenzione industriale. Questo approccio si basa sull'analisi avanzata dei dati per prevedere quando un componente o un sistema potrebbe guastarsi, consentendo interventi mirati prima che si verifichino problemi. L'obiettivo è passare da una manutenzione basata su intervalli fissi a una manutenzione basata sulle effettive condizioni dell'impianto, ottimizzando così tempi e costi degli interventi.
Sensori IoT per il monitoraggio in tempo reale
L'Internet of Things (IoT) ha rivoluzionato il modo in cui raccogliamo dati sulle prestazioni degli impianti. Sensori avanzati, installati su componenti critici, forniscono un flusso continuo di informazioni su parametri chiave come temperatura, vibrazione, pressione e consumo energetico. Questi dati in tempo reale permettono di identificare precocemente anomalie e trend di deterioramento, consentendo una pianificazione più accurata degli interventi manutentivi.
L'implementazione di una rete di sensori IoT richiede una pianificazione attenta e una strategia di integrazione con i sistemi esistenti. È fondamentale selezionare i punti di monitoraggio più significativi e definire soglie di allarme appropriate per ciascun parametro monitorato. La sfida sta nel bilanciare la quantità di dati raccolti con la capacità di analizzarli efficacemente, evitando il sovraccarico informativo.
Machine learning applicato alla previsione dei guasti
Il machine learning rappresenta uno strumento potente per estrarre valore dai big data generati dai sensori IoT. Algoritmi di intelligenza artificiale possono analizzare enormi quantità di dati storici e in tempo reale per identificare pattern e correlazioni non evidenti all'occhio umano. Questi modelli predittivi possono anticipare con notevole precisione quando un componente si sta avvicinando al punto di guasto, consentendo interventi tempestivi.
L'applicazione del machine learning alla manutenzione predittiva richiede una collaborazione stretta tra esperti di dominio e data scientist. È cruciale addestrare i modelli con dati di alta qualità e validare costantemente le loro previsioni con l'esperienza sul campo. Man mano che il sistema apprende, la sua accuratezza predittiva migliora, portando a una pianificazione sempre più efficiente degli interventi manutentivi.
Dashboard di manutenzione basate su KPI specifici
Le dashboard di manutenzione moderne offrono una visione d'insieme delle performance degli impianti e dell'efficacia delle strategie manutentive. Queste interfacce visualizzano in tempo reale i Key Performance Indicator (KPI) più rilevanti, come il Mean Time Between Failures (MTBF), il Mean Time To Repair (MTTR) e l'Overall Equipment Effectiveness (OEE). La visualizzazione intuitiva di questi dati permette ai manager di prendere decisioni informate e tempestive sulla gestione degli asset.
La progettazione di dashboard efficaci richiede una profonda comprensione dei processi aziendali e degli obiettivi strategici. È importante selezionare un set di KPI bilanciato che rifletta sia l'efficienza operativa che l'impatto finanziario delle attività manutentive. Le dashboard dovrebbero anche fornire la possibilità di drill-down nei dati, consentendo analisi più dettagliate quando necessario.
Integrazione con sistemi ERP e CMMS
L'integrazione dei dati provenienti dalla diagnostica predittiva con i sistemi ERP (Enterprise Resource Planning) e CMMS esistenti è fondamentale per massimizzare il valore delle informazioni raccolte. Questa integrazione permette di automatizzare la generazione di ordini di lavoro, la gestione dell'inventario dei ricambi e la pianificazione delle risorse umane in base alle previsioni di manutenzione.
La sfida principale nell'integrazione di questi sistemi sta nella standardizzazione dei dati e nella creazione di interfacce robuste tra piattaforme spesso eterogenee. È essenziale definire protocolli chiari per lo scambio di informazioni e assicurare che i dati critici siano accessibili in tempo reale a tutti gli stakeholder coinvolti nel processo manutentivo.
Procedure standardizzate di manutenzione secondo le norme ISO 55000
L'adozione di procedure standardizzate di manutenzione, allineate con le norme ISO 55000 sulla gestione degli asset, rappresenta un passo fondamentale verso l'eccellenza operativa. Queste norme forniscono un framework completo per l'implementazione di un sistema di gestione degli asset efficace e sostenibile, coprendo l'intero ciclo di vita degli impianti industriali.
Le procedure standardizzate secondo ISO 55000 si concentrano su diversi aspetti chiave:
- Definizione di una politica e di una strategia di gestione degli asset allineate con gli obiettivi aziendali
- Implementazione di processi decisionali basati sul rischio e sul valore
- Sviluppo di piani di manutenzione coerenti e integrati
- Monitoraggio continuo delle performance e miglioramento dei processi
L'implementazione di queste procedure richiede un cambiamento culturale all'interno dell'organizzazione, promuovendo una visione olistica della gestione degli asset e una maggiore collaborazione tra i diversi dipartimenti. È fondamentale coinvolgere tutti i livelli dell'organizzazione, dalla dirigenza agli operatori sul campo, per garantire il successo dell'adozione di queste pratiche standardizzate.
Formazione del personale tecnico sulle nuove tecnologie manutentive
La rapida evoluzione delle tecnologie manutentive richiede un investimento continuo nella formazione del personale tecnico. Le competenze richieste oggi vanno ben oltre le tradizionali abilità meccaniche ed elettriche, includendo conoscenze in ambiti come l'analisi dei dati, l'IoT e l'intelligenza artificiale. Un programma di formazione efficace deve bilanciare l'aggiornamento delle competenze tecniche specifiche con lo sviluppo di soft skills come il problem-solving e la capacità di lavorare in team multidisciplinari.
La formazione dovrebbe essere strutturata in modo da coprire diversi livelli di competenza, dal personale operativo ai manager di manutenzione. Metodologie di apprendimento innovative come la realtà aumentata e i simulatori virtuali possono accelerare il processo di acquisizione delle competenze, offrendo esperienze pratiche in un ambiente sicuro e controllato.
La formazione continua del personale tecnico non è un costo, ma un investimento strategico per mantenere la competitività in un mercato in rapida evoluzione.
È inoltre essenziale sviluppare programmi di mentoring e condivisione delle conoscenze all'interno dell'organizzazione, per preservare e trasmettere l'esperienza accumulata dai tecnici più esperti alle nuove generazioni di professionisti della manutenzione.
Gestione dell'obsolescenza dei componenti critici
La gestione dell'obsolescenza dei componenti critici rappresenta una sfida significativa per molte industrie, specialmente in settori con cicli di vita degli impianti molto lunghi. L'obsolescenza può manifestarsi non solo a livello hardware, ma anche software, con sistemi di controllo che diventano incompatibili con le nuove tecnologie. Una strategia proattiva di gestione dell'obsolescenza è essenziale per garantire la continuità operativa e ottimizzare i costi di manutenzione nel lungo periodo.
Analisi del ciclo di vita degli asset industriali
L'analisi del ciclo di vita degli asset industriali è il punto di partenza per una gestione efficace dell'obsolescenza. Questo processo coinvolge la valutazione sistematica di ogni componente critico, considerando fattori come la disponibilità futura di ricambi, il supporto del produttore e l'evoluzione tecnologica del settore. L'obiettivo è identificare in anticipo i componenti a rischio di obsolescenza e pianificare interventi mirati.
Un approccio strutturato all'analisi del ciclo di vita dovrebbe includere:
- Creazione di un inventario dettagliato degli asset critici
- Valutazione del rischio di obsolescenza per ciascun componente
- Sviluppo di piani di mitigazione specifici
- Monitoraggio continuo dello stato di obsolescenza
L'utilizzo di software specializzati per la gestione del ciclo di vita degli asset può automatizzare gran parte di questo processo, fornendo alert tempestivi quando un componente si avvicina alla fine del suo ciclo di vita supportato.
Strategie di approvvigionamento per ricambi obsoleti
Gestire l'approvvigionamento di ricambi per componenti obsoleti richiede una strategia ben ponderata. Le opzioni includono l'acquisto anticipato di scorte (last-time buy), la ricerca di fornitori alternativi o l'esplorazione di soluzioni di reverse engineering. Ogni approccio ha i suoi pro e contro in termini di costi, rischi e impatto operativo.
Una strategia efficace di approvvigionamento per ricambi obsoleti dovrebbe considerare:
- L'analisi costi-benefici di ciascuna opzione di approvvigionamento
- La valutazione dei rischi associati all'utilizzo di parti non originali
- La possibilità di collaborazioni con altre aziende del settore per condividere scorte di ricambi critici
- L'esplorazione di soluzioni innovative come la stampa 3D per la produzione on-demand di componenti specifici
È fondamentale mantenere una comunicazione aperta con i fornitori storici e monitorare costantemente il mercato per identificare nuove fonti di approvvigionamento o tecnologie alternative.
Retrofitting e upgrade tecnologico degli impianti esistenti
Il retrofitting e l'upgrade tecnologico rappresentano spesso la soluzione più efficace per estendere la vita utile degli impianti esistenti, migliorandone al contempo le prestazioni. Questi interventi possono variare dalla semplice sostituzione di componenti obsoleti con equivalenti moderni fino alla completa riprogettazione di sistemi di controllo e automazione.
Un progetto di retrofitting ben pianificato può offrire numerosi vantaggi:
- Miglioramento dell'efficienza energetica
- Aumento della produttività e della qualità del prodotto
- Riduzione dei costi di manutenzione nel lungo periodo
- Conformità con nuovi standard di sicurezza e ambientali
La chiave per il successo di un progetto di retrofitting sta nella pianificazione dettagliata e nella valutazione accurata dell'impatto su tutti gli aspetti del processo produttivo. È essenziale coinvolgere fin dalle prime fasi tutti gli stakeholder, dai tecnici di manutenzione agli operatori di linea, per garantire che l'upgrade soddisfi le reali esigenze operative e sia facilmente integrabile nei flussi di lavoro esistenti.
Impatto economico della manutenzione proattiva sul TCO
L'adozione di strategie di manutenzione proattiva ha un impatto significativo sul Total Cost of Ownership (TCO) degli asset industriali. Mentre l'implementazione di tecnologie avanzate e programmi di formazione richiede un investimento iniziale, i benefici a lungo termine in termini di riduzione dei tempi di fermo, aumento della produttività e ottimizzazione dei costi operativi possono essere sostanziali.
Un'analisi dettagliata del TCO dovrebbe considerare non solo i costi diretti di manutenzione, ma anche l'impatto
di manutenzione, ma anche l'impatto indiretto sull'efficienza produttiva, la qualità del prodotto e la sicurezza operativa. Studi di settore hanno dimostrato che l'implementazione di strategie di manutenzione proattiva può portare a una riduzione del TCO fino al 30% nel corso del ciclo di vita di un impianto.
Alcuni dei principali benefici economici della manutenzione proattiva includono:
- Riduzione dei tempi di fermo non pianificati
- Estensione della vita utile degli asset
- Ottimizzazione dei costi energetici
- Minimizzazione delle scorte di ricambi
- Riduzione dei costi di manodopera per interventi di emergenza
Per quantificare accuratamente l'impatto economico della manutenzione proattiva, è essenziale implementare un sistema di tracciamento dei costi dettagliato. Questo dovrebbe includere non solo i costi diretti di manutenzione, ma anche metriche come il costo dell'inattività, l'impatto sulla qualità del prodotto e l'efficienza energetica. L'utilizzo di software avanzati di Asset Performance Management (APM) può facilitare questa analisi, fornendo una visione olistica delle performance degli asset e del loro impatto finanziario.
L'investimento in manutenzione proattiva non dovrebbe essere visto come un costo, ma come un driver strategico per l'ottimizzazione delle performance aziendali e la creazione di valore nel lungo periodo.
L'adozione di un approccio proattivo alla manutenzione, supportato da tecnologie avanzate e competenze specializzate, rappresenta un fattore chiave per garantire la competitività e la sostenibilità delle imprese industriali moderne. La capacità di anticipare e prevenire i problemi, ottimizzare le performance degli asset e ridurre i costi operativi nel lungo periodo si traduce in un vantaggio competitivo significativo in un mercato sempre più sfidante e dinamico.